Replacement and relocation of production line of Owens Corning fibreglass wallpaper
- Industriële verhuizingen
- Maak-industrie
- Machineverplaatsingen
Owens Corning has expanded its fibreglass wallpaper production capacity. The ACE (Apeldoorn Capacity Project Phase 2) project was launched for this purpose. Together with its partner Yourtech, Saan won the contract to relocate a winder and a rewinder. The old dryer was also removed and a new one installed. Because production was halted during the work, it was very important to Owens Corning that the work should take as little time as possible.
Work was started on the relocation of the machine that winds rolls of wallpaper on to smaller rolls. Saan and Yourtech disconnected the hydraulic system and lifted out the smaller parts with the existing overhead crane. The main frame removed was lifted with this crane and a 16-tonne Saan forklift truck, placed on a set of trolleys and moved to its new position. The cable ducts and the gap left by the unwinding block that had to be bypassed at this point were filled in beforehand for this. Once the main frame had been aligned, the other parts were fitted again. A number of new parts were also installed. During the work on the winder, Owens Corning continued production with the rest of the line.
The following week, work was started on relocating the rewinder. The big parts were moved with the overhead crane and Saan’s 16-tonne forklift truck. The delicate measuring system in the rewinder was lifted out and temporarily stored until it could be fitted in. The parts that were difficult to access were lifted with Saan’s minicrane. One week later, the various parts were put into their positions. Here a number of parts were adjusted. The old dryer, being 7 metres wide, 22 metres long and 6 metres high, was removed, as were all the parts located on it such as catwalks, valves and cable ducts.
Then beams were placed at six positions under the dryer, which weighed about 150 tonnes, in order to lift the entire unit with the 320-tonne Saan gantry crane. This was then set down on SPMT trucks and driven entirely outside, where it could be further dismantled. The 13 new parts were collected from Germany. Then over two days these were placed in the position of the old dryer and the rewinder. They were moved with the aid of a truck with a crane and the overhead crane. Under the supervision of the German supplier (VITS) the dryer with burners, extractor fans, chain guides, insulation panels, doors, rails etc. was further dismantled.
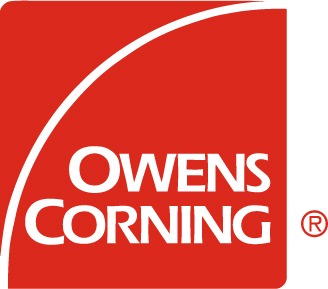