Removal King Nonwovens
- Complete bedrijfsverhuizingen
- Industriële verhuizingen
- Maak-industrie
King Nonwovens was founded by Directors Bart van der Hart and Jan van Leeuwen. As the name suggests, the company specialises in nonwovens, textiles consisting of synthetic and/or natural fibres bound together using a hi-tech manufacturing process. Nonwovens are found for example in furniture, in roof coverings, in horticulture and in cars. The business has grown steadily, eventually requiring more space: by the autumn of 2017 it was time to move to new premises. Jan van Leeuwen talks here about the experience of moving.
"As far as I am concerned this removal job went according to the book"
Saan’s offer for King Nonwovens’ removal came just in time. “When their Account Manager Robert Bos phoned me we were just on the point of giving the removal work to another firm,” says Jan. “I was curious about what Saan might have to offer, and I decided to give Robert time to submit a quotation. I quickly developed a positive feeling about Saan. Their price was higher, but the quotation looked highly professional. In fact their whole approach impressed me with its professionalism. Robert came along with a technical colleague from Saan and somebody from Yourtech, Saan’s partner company, who would be handling the coding, stripping down and reassembly of the machinery. They clearly knew what they were about, and they went to a lot of trouble to get the order. That was what decided me to get involved with Saan and Yourtech”.
King Nonwovens moved from Lelystad, where the firm had premises in various locations around the town, to a new-build site in Zeewolde. Jan: “We couldn’t find a really suitable location to build in Lelystad. But the place we found in Zeewolde met all our needs.” The impressive new building houses offices, production facilities and storage space. In total Saan and Yourtech were responsible for moving 25 office workspaces and 18 machines, several of which were dismantled, as well as a large quantity of stock. Despite the size of the new building, finding the right location for everything was a bit of a puzzle. Jan laughs: “After months of planning I was still moving machines around on the floor plan just before the move began. The layout was only finalised at the last moment.”
A well-oiled machine
The removal work started in November, with Saan and Yourtech working closely together. “You could see straight away that the people from Saan and Yourtech were completely tuned in to one another’s ways of working. Yourtech began with the coding, followed by the dismantling of machinery, so it was they who set the pace. Saan continually adapted their schedule in line with Yourtech’s work. It really was like a well-oiled machine!” says Jan van Leeuwen enthusiastically. “They only called me a couple of times during the removal process, which I took as a good sign. The move gave our technical man a few headaches: he has responsibility for all the machinery, and if something went wrong and a machine was damaged we would be looking at a lead time of a year before a replacement could be brought in. But two days into the move he was confident that everything was going to be ok.”
Less time needed than anticipated
“As far as I am concerned this removal job went according to the book,” says Jan contentedly. “There were a couple of hitches but these were quickly solved by Saan. There was a leak of oil from a forklift truck, but Saan immediately brought in a specialist cleaning firm to sort it out. And there was a bit of miscommunication between ourselves and one of the removal men during the office move near the end of the project, but in the end everything was moved smoothly and without issues. The machines actually didn’t stand idle for long at all, and the whole move took less time than we anticipated. All I can say is that I am highly satisfied with Saan and Youtech’s work on our relocation!”
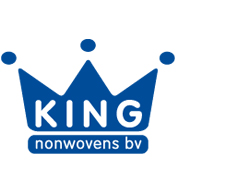