Lely Industries relocation of entire factory and warehouse
- Bedrijfsverhuizing
- Food
- Industriële verhuizingen
Lely Industries wanted to develop and produce its products in a sustainable environment. So the contract was awarded for the construction of a new main site, ‘de Lely Campus’ in Maassluis. This became one of the most sustainable industrial buildings in Europe. In this innovation campus, the fodder business, milk production and operations divisions were set up adjacent to each other. Saan was responsible for the relocation of the Rotterdam site to the new main site in Maassluis.
This new campus was a necessity for Lely Industries because of rapidly growing market demand and as a consequence of the growing number of employees. For this complex relocation Lely asked several relocation companies for a quotation. Saan’s approach, quotation and broad experience with similar relocations gave Lely the confidence to let Saan implement the relocation.
The relocation had to be carried out in four weeks during the summer holiday period and this deadline was easily met. The 180 trailer loads were transferred in over 3 weeks and Lely used the fourth week to unpack and connect everything. The transportation of the milking robots being built was provided by Saan with special means of transport. This allowed Lely’s employees to restart production immediately after the holiday.
The existing building for the production of machines for the fodder business, which was situated at Weverskade 60, was still functioning exceptionally well and it was linked to the new campus. Then the production of milking robots, stable/cowshed products and feeding equipment returned from Rotterdam to Maassluis. About 175 engineers in total were accommodated in the buildings. The new work environment offers employees even more space for creativity and innovation based on modern working methods such as ‘Work Smarter’ (Het Nieuwe Werken) and ‘Lean’. ‘Work Smarter’ must contribute to more efficient and effective collaboration so that Lely can achieve further growth.
Prior to the relocation, Saan managed a trial relocation to determine all the relocation procedures. A fixed project leader was appointed during preparation and implementation. So the client had one point of contact for the entire relocation. Many hundreds of pieces of bulky and complex production equipment and production lines were relocated to the new site and then Saan looked after the relocation of the development departments, laboratories, racks and stocks.
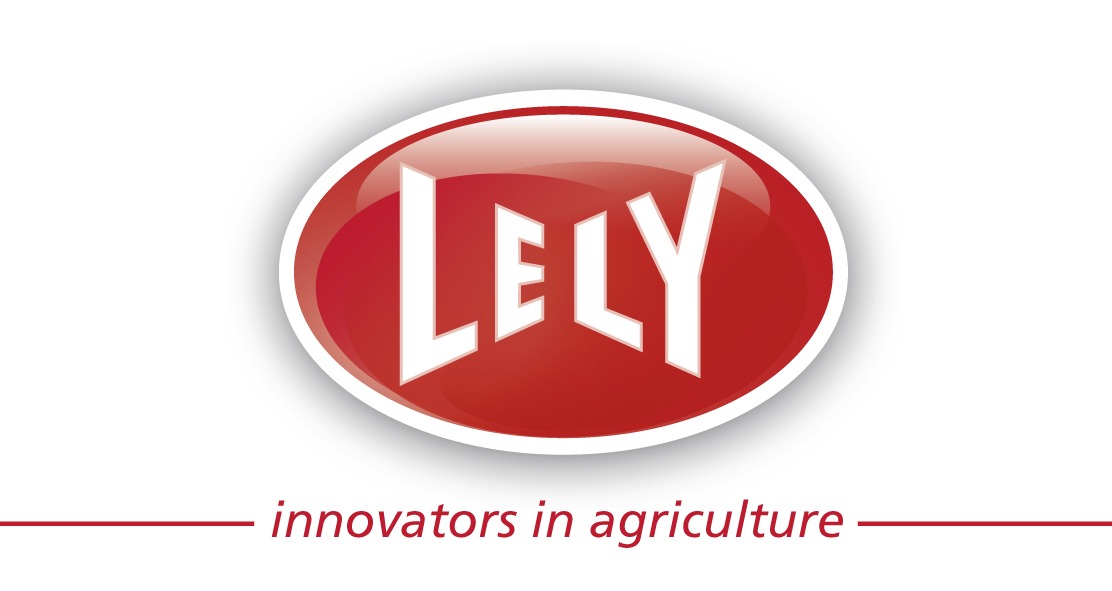